How ball valves are made: materials, precision, and quality steps
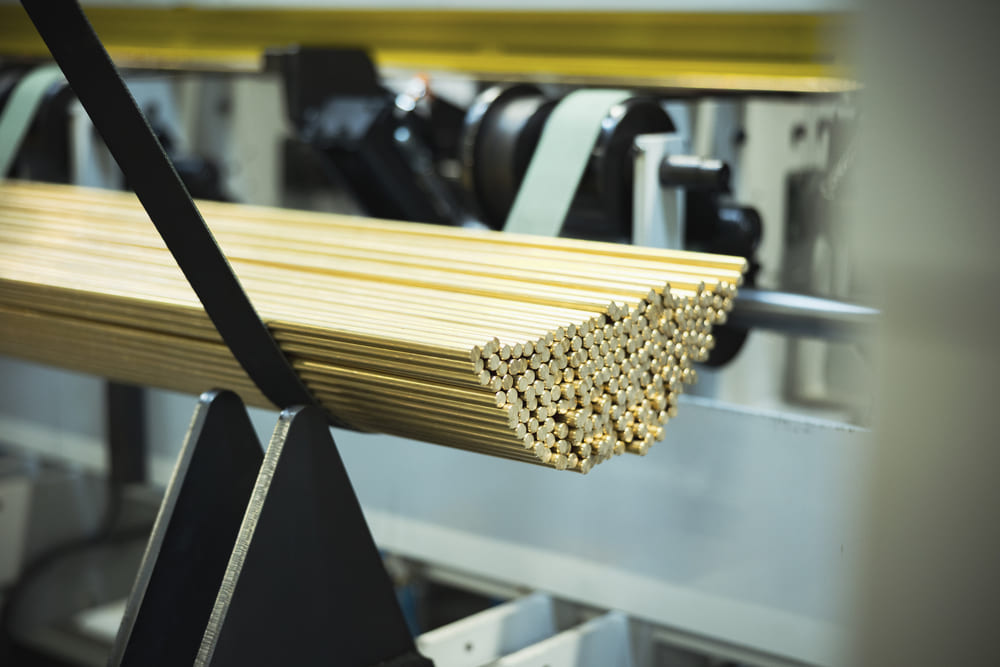
Understanding the ball valve manufacturing process is essential for professionals seeking long-term performance, safety and reliability in fluid control systems. Whether used in plumbing, HVAC, industrial or gas applications, the quality and precision of a ball valve directly affect system integrity and efficiency. At RuB Inc., our commitment to quality begins at the source — with raw material selection — and continues through every step of production, testing and packaging. Each stage is designed to meet the most rigorous industry standards in durability, functionality and traceability.
In this guide, we take you through the complete process of how ball valves are made, with a special focus on our precision brass ball valve manufacturing process.
Step 1: Raw material selection and quality control
The process begins with the careful selection of raw materials. In particular, RuB Inc. uses certified brass bars sourced within a 30 miles radius from our plant, that comply with stringent quality and safety standards. Every batch is tested for chemical composition and mechanical properties to ensure consistent machinability and performance.
Step 2: Machining and threading
Next phase is hot forging. Solid brass bars are heated to controlled temperature and pressed in precision dies to form the desired shape: typically valve body, end-cap, ball. Forging ensures structural integrity, optimal grain alignment, and material density — critical factors in how ball valves perform withstanding pressure and long-term use.
Step 3: Valve body machining
Forged bodies move on to precision machining. This key phase in the ball valve manufacturing process includes boring the internal flow path, machining the stem hole and threading the pipe connections (NPT, BSPT, ISO, solder, etc.). Tight tolerances are maintained throughout to guarantee leak-free assembly long-standing performance and compatibility with actuators or manual controls.
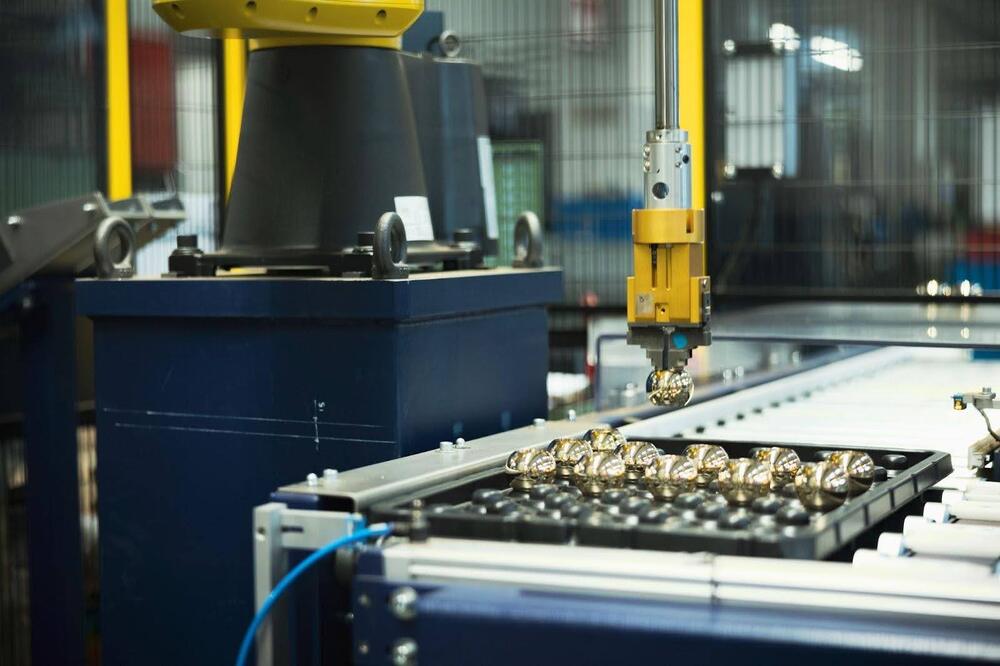
Step 4: Valve ball manufacturing and surface finishing
The manufacturing process to make a valve ball involves shaping solid brass into a sphere using advanced turning and polishing techniques. The brass ball is then nickel-chrome plated to minimize friction, enhance corrosion resistance, and provide smooth movement within the seats. This step plays a vital role in achieving consistent flow control and tight sealing, which are essential to valve performance and reliability. Each ball is visually inspected and measured for perfect roundness.
Step 5: Seat and seal installation in brass ball valves
Once core components are ready, the next step in the ball valve manufacturing process is seat and seal assembly. RuB Inc. uses high-quality PTFE or elastomeric materials into the valve body to guarantee reliable shutoff performance and ease of operation. Materials chosen and cleanliness of assembly ensure wide chemical resistance and longevity in various temperature and pressure conditions.
Step 6: Stem assembly and blowout-proof feature
The stem is inserted into the valve neck and connects to the ball once this is assembled. Blowout-proof feature is an essential part of operational safety offered by RuB design. Sealing is granted by either double O-ring or packing system.
Step 7: 100% seal test and inspection
Application of stringent quality assurance criteria is critical in any product. Every RuB Inc. valve undergoes 100% seal test using hydrostatic or pneumatic systems and automated readers that dictate whether the single valve is good for our customers or needs to be scrapped. The brass ball valve manufacturing process also includes torque testing, dimensional inspections and functional cycling to ensure consistent performance. Once valves pass testing, handle is then fitted and operated to ensure smooth 90° rotation.
Step 8: Marking and packaging of finished ball valves
As part of the final step, each valve is marked via laser engraving; if required by customer, customer logo can be applied or other markings. Products are then packed in solid boxes, then cartons, put on shrink-wrapped pallets to ensure they arrive in perfect condition. The whole packaging and storing system is highly automated and guided by bar-codes.
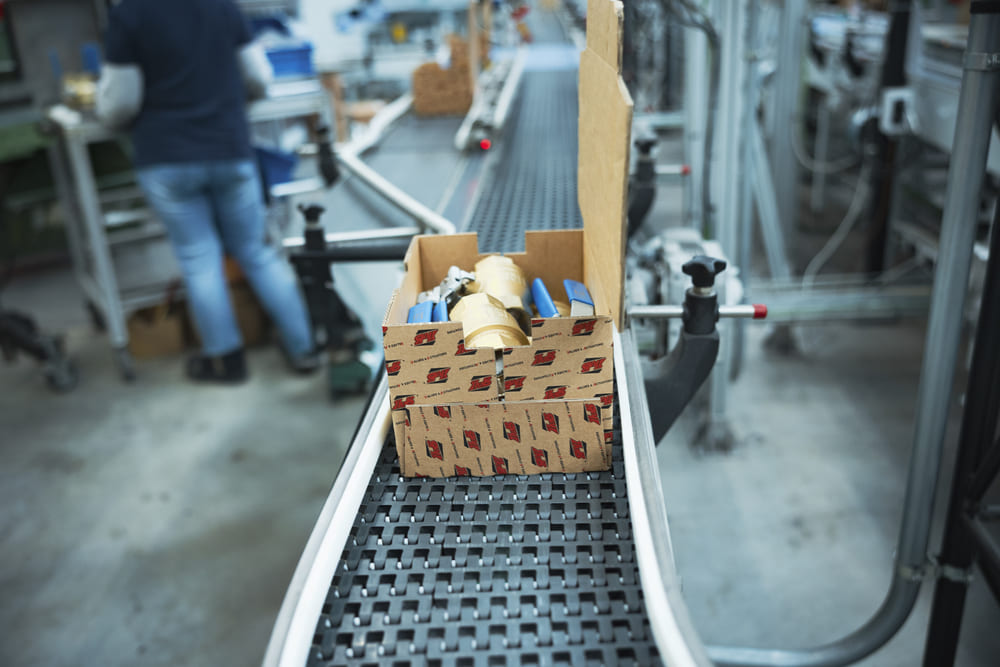
Quality assurance in the RuB Inc. ball valve manufacturing process
At RuB Inc., we take pride in our vertically integrated production process. We pay close attention to the quality of every component, from raw materials to clean assemblies and testing, ensuring that each part contributes to the overall reliability and performance of our valves. Every phase of the process is designed to meet the highest industry standards, with a strong emphasis on precision, durability and traceability. Our plant is fully certified according to major international standards, including ISO 9001, ISO 14001, and ISO 45001. These certifications reflect our ongoing commitment to quality management, environmental responsibility and workplace safety.
Whether you’re specifying for plumbing, HVAC, industrial automation or gas systems, RuB valves offer unmatched reliability backed by decades of engineering production experience and manufacturing expertise.
Are you looking for more information about our manufacturing capabilities or would you like a quote? Contact RuB Inc. team to discover how we can assist you with expert guidance, precision components, and end-to-end manufacturing support for your next project.